Minasoft Repairs provides a complete framework for managing product repair operations inside your company. Whether you service your own assets or offer repairs to customers, this module helps you track every stage—from initial request to completion.
Track every repair. Recover every cost.
What Repairs can do for you?
Whether you manufacture, distribute, or sell physical products, repairs are often part of your customer experience or internal asset lifecycle. Minasoft Repairs allows your teams to handle repair processes with structure and visibility—tracking diagnostics, part replacements, labor, and outcomes.
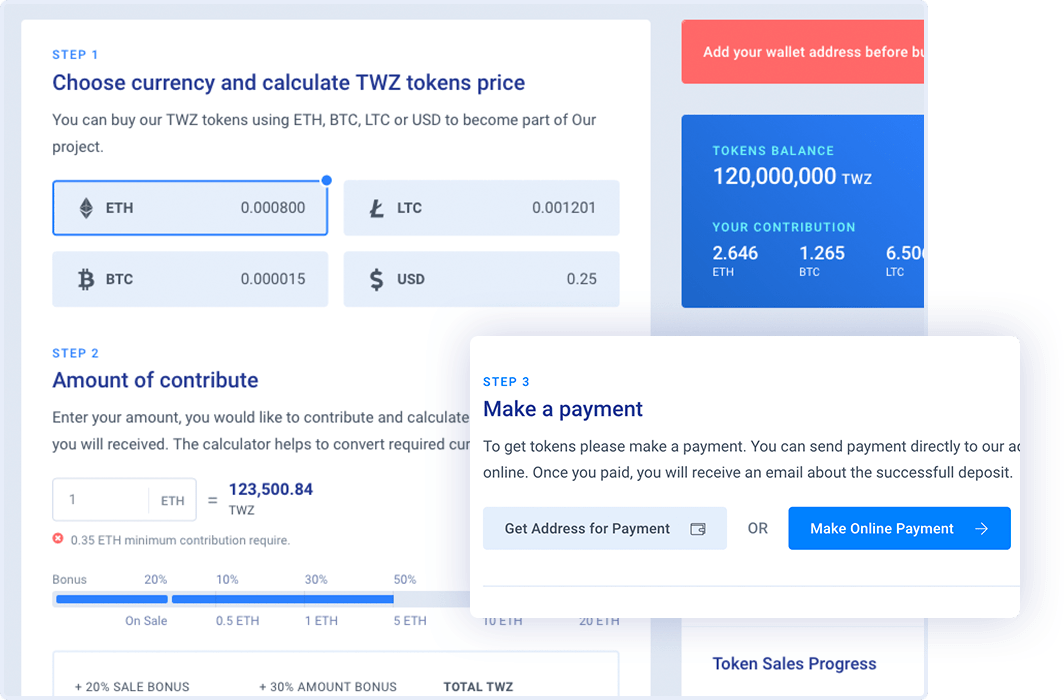
Structured Repair Order Management
At the core of Minasoft Repairs is a powerful repair order system that gives you control over every stage of the repair process. From product intake and diagnostics to part replacement, reassembly, and quality check, each step is documented.
From broken products to maintenance needs, Minasoft Repairs gives you a clear system for documenting repairs, assigning technicians, consuming parts, and billing clients. No spreadsheets, no guesswork—just a streamlined process that keeps operations smooth and customers satisfied.
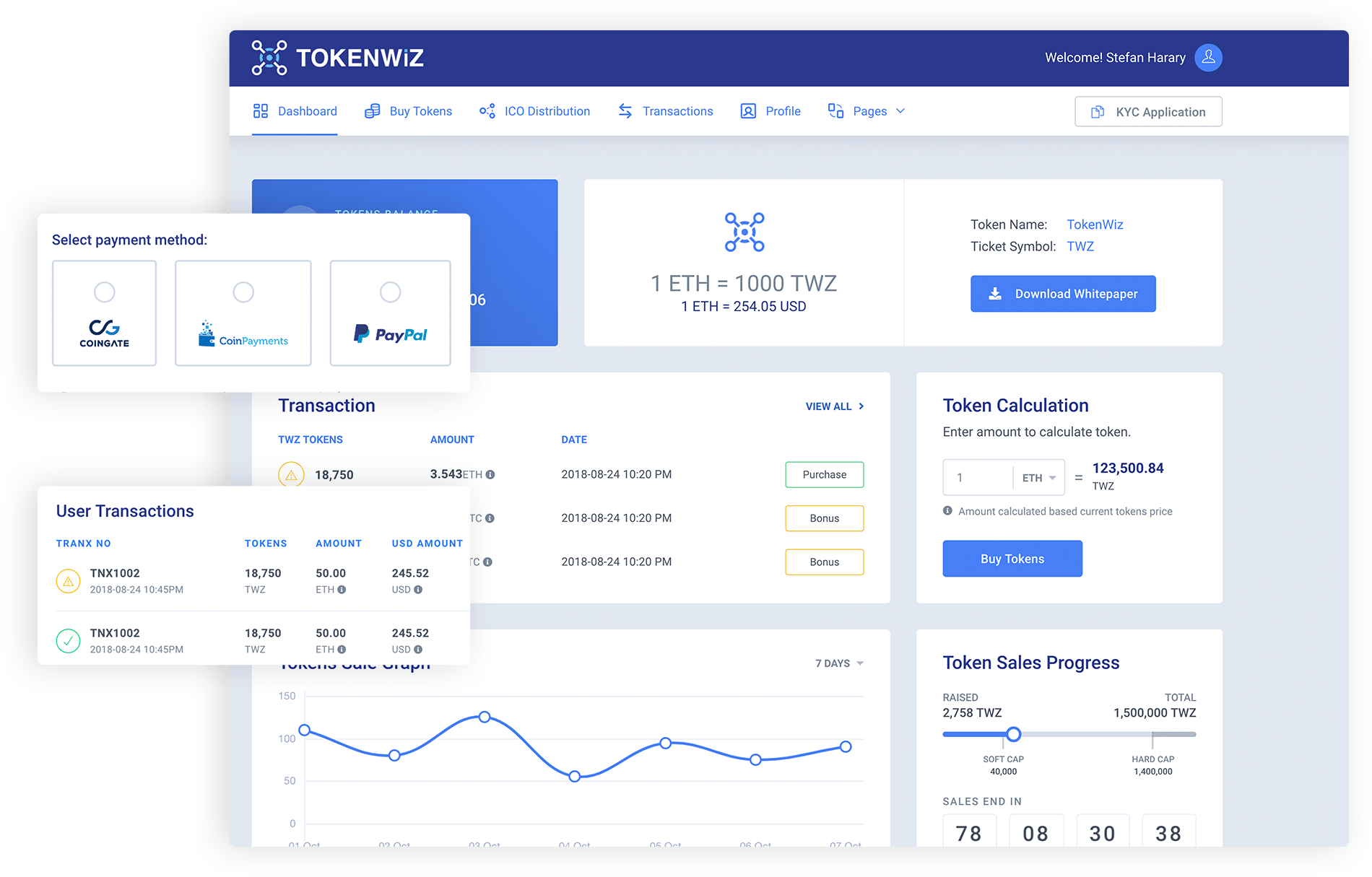
Complete Repair Lifecycle Management
Create repair orders, track used parts, define labor costs, and generate invoices with full integration to inventory, sales, and accounting. It's ideal for service centers, manufacturers, or any business with after-sales responsibilities.
Track Full Repair Lifecycle
Manage every repair from intake to delivery
Use and Replace Components
Consume inventory parts for accurate costing
Integrated Invoicing
Bill customers directly from repair operations
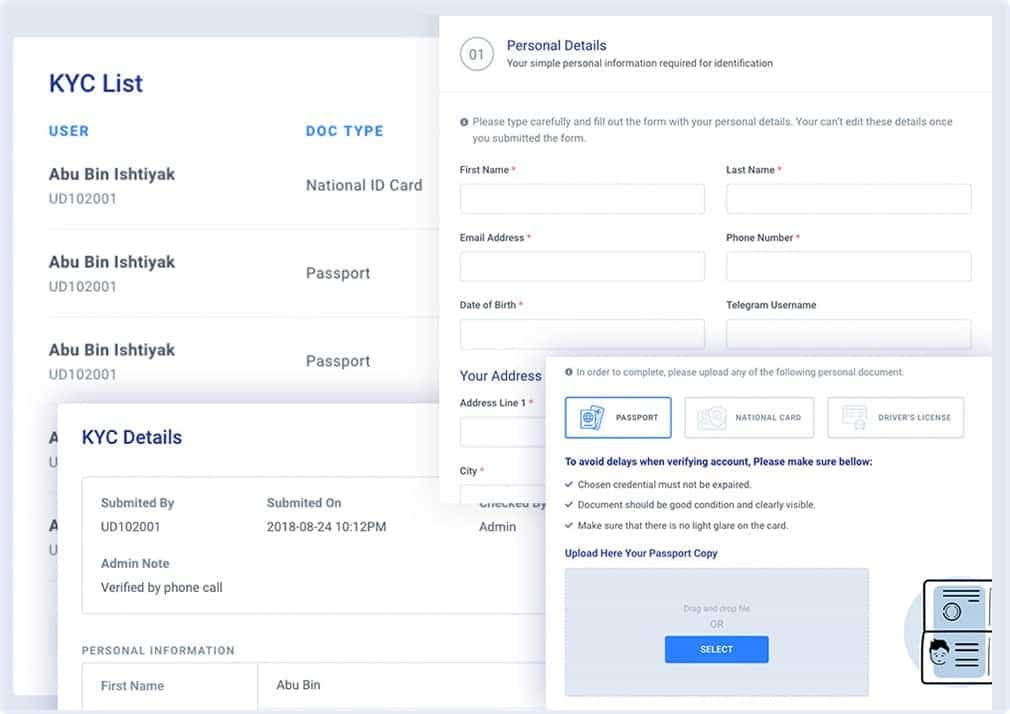
Repair Order Creation & Tracking
Create structured repair orders that include the product, customer, description of the problem, and assigned technician. Track status as the job progresses through every stage of the repair process.
- Register internal or customer repairs with full documentation
- Assign repair teams and deadlines for better coordination

Component Replacement and Cost Control
Use components from inventory during repairs, or replace defective parts with new ones. Inventory is adjusted automatically to maintain stock accuracy while tracking all costs and profitability.
- Log replaced and consumed parts automatically
- Track inventory movements with real-time stock impact
- Define labor and part costs with margin calculations
- Support for serial and lot numbers for full traceability
Stop losing money on untracked repairs.
Manage, cost, and bill repairs in a single streamlined system.
Get Started with Minasoft RepairsCan I manage both customer and internal repairs?
Yes. Minasoft Repairs allows you to manage customer-facing repairs (with invoicing and communication) and internal equipment maintenance. You can configure whether a repair is billable or purely operational, adapting the workflow to each scenario.
Is it possible to track parts used in a repair?
Absolutely. Every component used during a repair is logged and deducted from inventory automatically. You can distinguish between consumed items and those replaced, ensuring full traceability and correct stock valuation.
How do I bill a customer for a repair?
Once a repair is completed, you can generate an invoice directly from the repair order, including parts, labor, and additional fees. This invoice is fully integrated with your accounting and customer records.
Can I assign repairs to technicians or teams?
Yes. Each repair order can be assigned to a specific user or team. You can add deadlines, responsibilities, and internal notes to streamline communication and task management.
What happens if a repair involves serial-tracked items?
Minasoft Repairs supports serialized products. You can register the serial number of the item being repaired and maintain history of the intervention—critical for warranty claims, audit trails, or product lifecycle control.
Can I control repair profitability?
Yes. The system captures all costs (labor, components) and links them to the revenue generated from invoicing. You can analyze profitability per repair or across time, helping you refine pricing strategies and service delivery.
Is there a way to print a repair summary for the customer?
Yes. You can generate and customize repair confirmation reports including product info, work performed, parts replaced, pricing, and notes. These can be printed or sent digitally.
What visibility do I get over the repair lifecycle?
Each repair follows a clear workflow with statuses and audit logs. You can see who worked on it, what was done, which parts were used, and when the job was completed or delivered.
How does it integrate with other modules?
Minasoft Repairs integrates seamlessly with Inventory (for parts usage), Sales (for invoicing), and Accounting (for cost and revenue booking). It also connects with Employees and CRM for technician management and customer history.
Can I use the module to handle returns or warranty repairs?
Yes. You can flag repairs as under warranty and bypass invoicing if needed. Combine this with return orders and sales workflows to manage the full reverse logistics process.
How are warehouse impacts handled?
All movements caused by repairs—such as part consumption or finished goods re-entry—are logged in the warehouse. Inventory valuation and location tracking are fully integrated with your stock management system.
Can I track labor and service fees separately?
Yes. You can add manual or predefined service lines to a repair order, such as diagnostics, labor hours, or fixed fees. These are included in the cost structure and can be invoiced automatically with full accounting integration.
How does customer communication work?
Maintain open communication with your customers through notes and email templates. Let them know when repairs are received, completed, or delivered—improving trust and transparency throughout the process.
Is there quality control built into the process?
Before closing a repair, technicians can run a quality check and log results. You can define required tests or visual inspections to ensure the repaired product meets standards before delivery.
Can I customize repair workflows for different industries?
Yes. Whether you're in consumer electronics, automotive, manufacturing, or home appliances, you can customize workflows, status tracking, and documentation to match your specific industry requirements and service standards.
How is final delivery and handover managed?
Once the repair is completed, mark the order as delivered and optionally register a delivery signature or internal confirmation. This final step ensures traceability and accountability throughout the entire repair process.
Industries
Our repair management system adapts to various industries, providing specialized solutions for different business needs and repair processes.
How does the system handle laptop and phone repairs?
Track laptop, phone, or device repairs with precision. Manage part replacements, service history, and customer invoicing—perfect for electronics service centers or resellers.
What repair tracking features are available?
Our system provides comprehensive tracking for device diagnostics, part inventory management, repair status updates, and automated customer notifications throughout the repair process.
How does invoicing work for electronics repairs?
Generate detailed invoices with parts costs, labor charges, and service fees. Integration with payment systems ensures smooth transaction processing for your electronics service center.
How does the system manage vehicle repairs?
Handle vehicle or machinery repair processes in a structured way. Control parts usage, labor cost, and integrate repairs with fleet or asset management modules.
What fleet management integration is available?
Seamlessly integrate with fleet management systems to track maintenance schedules, repair history, and vehicle downtime. Monitor costs and optimize fleet performance across your entire vehicle inventory.
How are labor costs calculated for automotive repairs?
Track technician time, apply hourly rates, and calculate total labor costs automatically. Include parts markup, diagnostic fees, and generate comprehensive repair estimates for customers.
How does the system support manufacturing maintenance?
Manage internal maintenance of machinery and equipment. Keep production running smoothly by logging repair needs, technician work, and downtime resolution.
How is production downtime tracked?
Monitor equipment downtime in real-time, track repair duration, and analyze maintenance patterns to minimize production interruptions and optimize manufacturing efficiency.
What preventive maintenance features are available?
Schedule regular maintenance tasks, set up automated alerts for service intervals, and maintain detailed equipment service records to prevent unexpected breakdowns and extend machinery life.
How does the system handle professional tool repairs?
Offer repair services for professional-grade tools and machinery. Manage warranties, diagnose issues, and standardize your parts and labor billing.
What warranty management features are included?
Track warranty periods, manage warranty claims, and automatically apply warranty coverage to eligible repairs. Maintain detailed warranty records for compliance and customer service.
How are diagnostic procedures standardized?
Create standardized diagnostic checklists, document repair procedures, and maintain consistent service quality across your team. Generate detailed diagnostic reports for customers and internal use.
How does the system manage appliance service centers?
Service centers can manage in-warranty and post-warranty appliance repairs, track components, and provide customers with full transparency through structured repair orders.
What customer transparency features are available?
Provide customers with real-time repair status updates, detailed service reports, and transparent pricing. Send automated notifications at each repair milestone to keep customers informed.
How are warranty and post-warranty repairs differentiated?
Automatically identify warranty status, apply appropriate pricing structures, and manage different service levels for in-warranty versus post-warranty repairs with clear documentation and billing processes.